Automatic recessed Filter Press anti leakage filter press
✧ Product Description
It is a new type of the filter press with the recessed filter plate and strengthen rack.
There are two kinds of such filter press: PP Plate Recessed Filter Press and Membrane Plate Recessed Filter Press.
After the filter plate has been pressed,there will be a closed state among the chambers to avoid the liquid leakage and odors volatilization during the filtration and cake discharging.
It is widely used in the pesticide, chemical, the strong acid / alkali/corrosion and the volatile industries, etc.
✧ Product Features
A、Filtration pressure: 0.6Mpa----1.0Mpa----1.3Mpa-----1.6mpa (for choice)
B、Filtration temperature:45℃/ room temperature; 80℃/ high temperature; 100℃/ High temperature. The raw material ratio of different temperature production filter plates is not the same, and the thickness of filter plates is not the same.
C、Liquid discharge method - close flow:Under the feed end of the filter press, there are two close flow outlet main pipes, which are connected with the filtrate recovery tank. If the liquid needs to be recovered, or if the liquid is volatile, smelly, flammable and explosive, close flow is better.
D-1、Selection of filter cloth material: The pH of the liquid determines the material of the filter cloth. PH1-5 is acidic polyester filter cloth, PH8-14 is alkaline polypropylene filter cloth. The viscous liquid or solid is preferred to choose twill filter cloth, and the non-viscous liquid or solid is selected plain filter cloth.
D-2、Selection of filter cloth mesh: The fluid is separated, and the corresponding mesh number is selected for different solid particle sizes. Filter cloth mesh range 100-1000 mesh. Micron to mesh conversion (1UM = 15,000 mesh---in theory).
E、Rack surface treatment: When PH value neutral or weak acid base, the surface of the filter press beam is sandblasted first, and then sprayed with primer and anti-corrosion paint. When the PH value is strong acid or strong alkaline, the surface of the filter press frame is sandblasted, sprayed with primer, and wrapped with stainless steel or PP plate.
F、Filter cake washing: When solids need to be recovered, the filter cake is strongly acidic or alkaline; When the filter cake needs to be washed with water, please send an email to inquire about the washing method.
G、Filter press feeding pump selection: The solid-liquid ratio, acidity, temperature and characteristics of the liquid are different, so different feed pumps are required. Please send email to inquire.
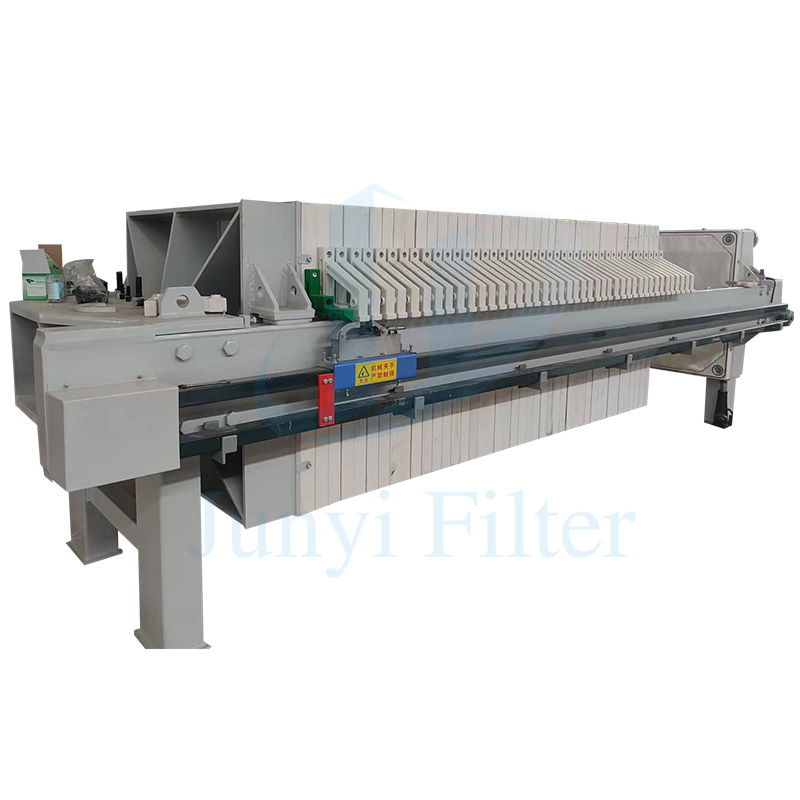
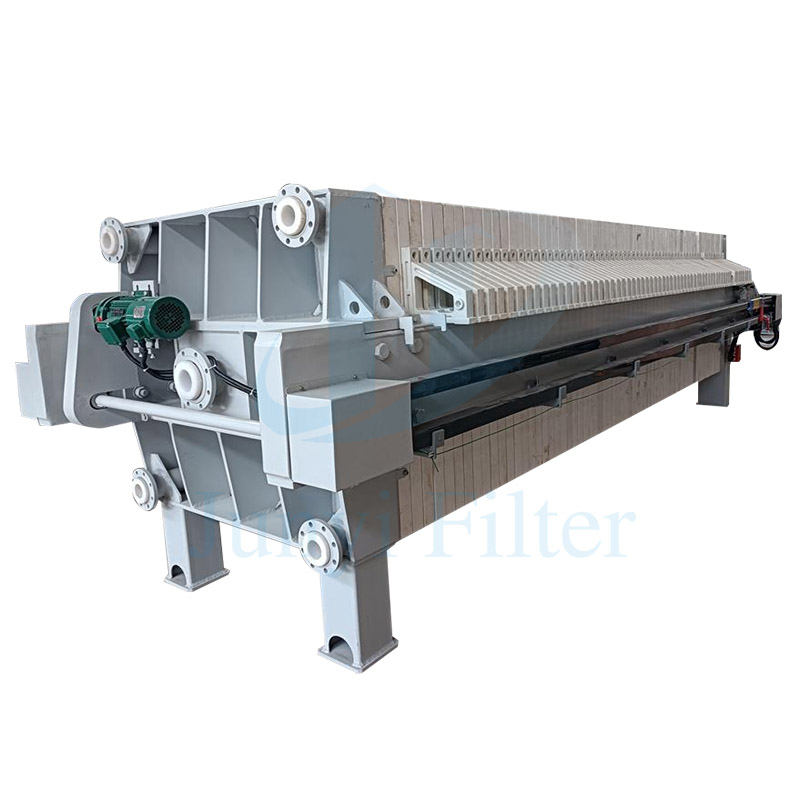
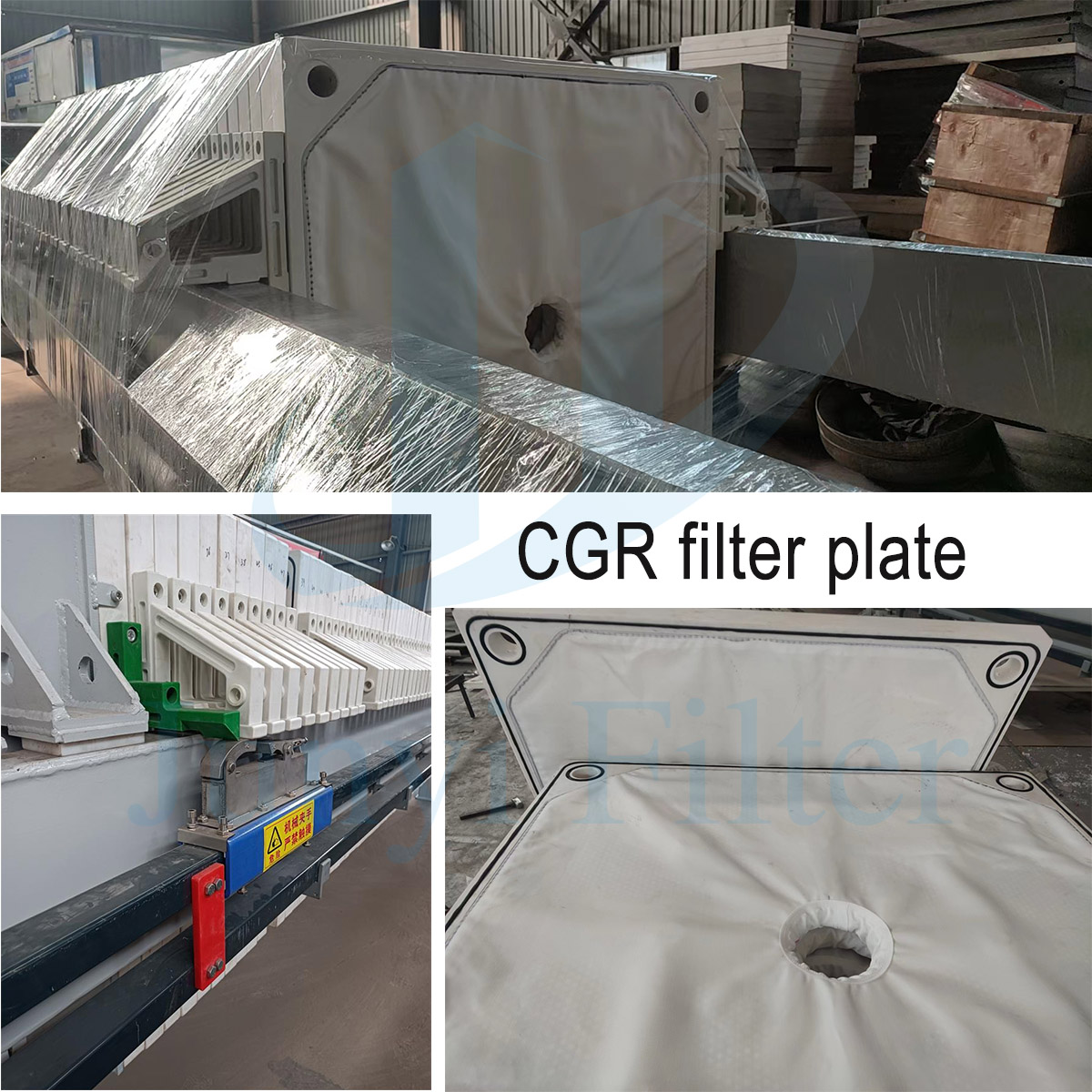
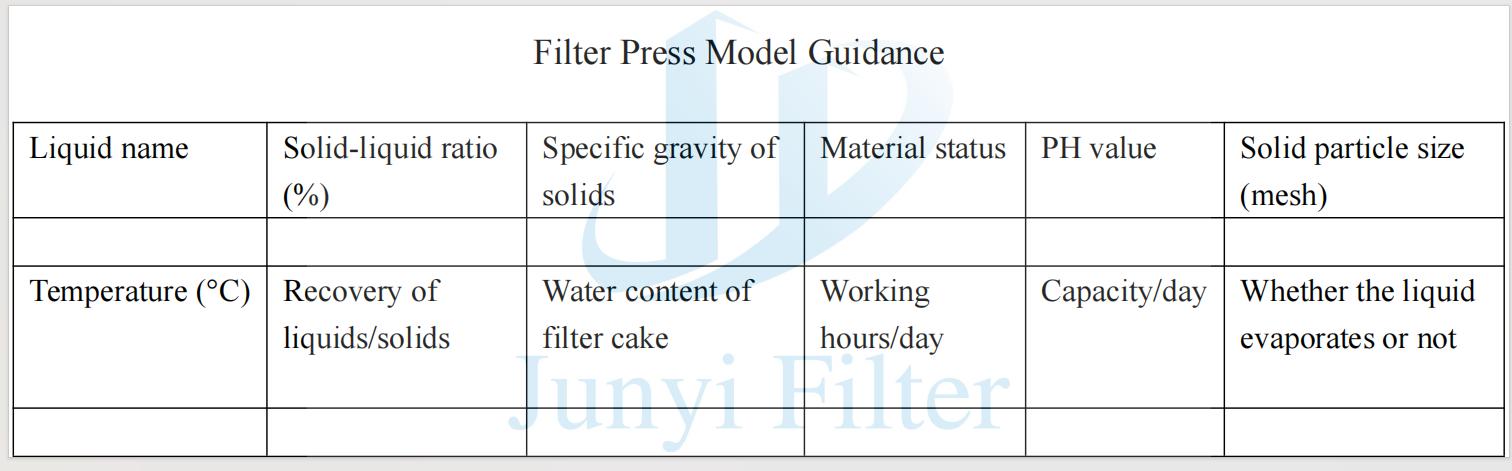
✧ Feeding Process
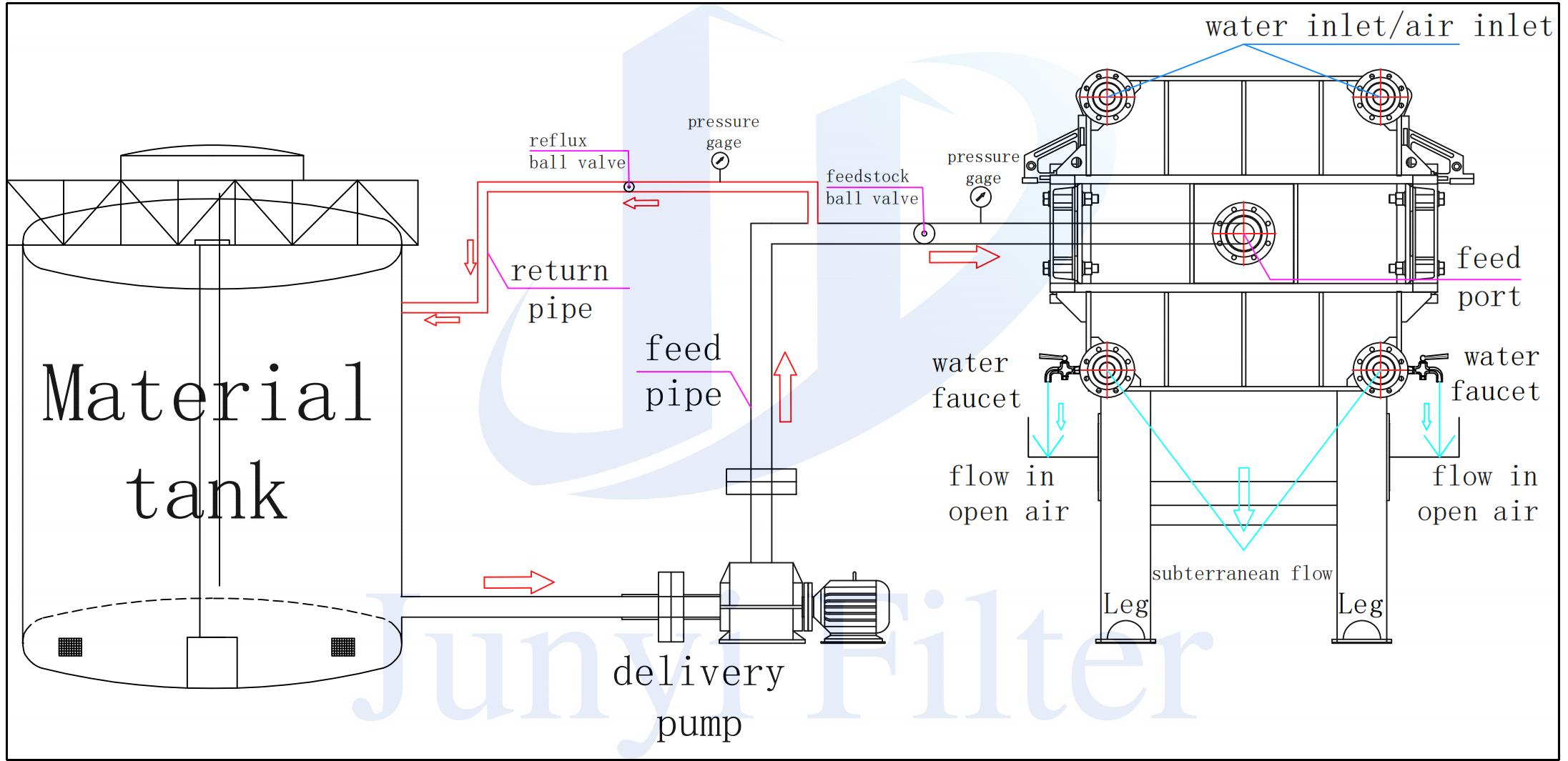
✧ Application Industries
It is widely used in solid-liquid separation process in petroleum, chemical, dyestuff, metallurgy, pharmacy, food, coal washing, inorganic salt, alcohol, chemical, metallurgy, pharmacy, light industry, coal, food, textile, environmental protection, energy and other industries.
✧ Filter Press Ordering Instructions
1. Refer to the filter press selection guide, filter press overview, specifications and models, select the model and supporting equipment according to the needs.
For example: Whether the filter cake is washed or not, whether the filtrate is open (seen flow) or close (unseen flow), whether the rack is corrosion-resistant or not, the mode of operation, etc., must be specified in the contract.
2. According to the special needs of customers, our company can design and produce non-standard models or customized products.
3. The product pictures provided in this document are for reference only. In case of changes, we will not give any notice and the actual order will prevail.
✧ Requirements for use of filter press
1. According to the process requirements to make pipeline connection, and do water inlet test, detect the air tightness of the pipeline;
2. For the connection of the input power supply (3 phase + neutral), it is best to use a ground wire for the electric control cabinet;
3. Connection between control cabinet and surrounding equipment. Some wires has been connected. The output line terminals of the control cabinet are labeled. Refer to the circuit diagram to check the wiring and connect it. If there is any looseness in the fixed terminal, compress again;
4. Fill the hydraulic station with 46 # hydraulic oil, the hydraulic oil should be seen in the tank observation window. If the filter press operates continuously for 240 hours, replace or filter the hydraulic oil;
5. Installation of cylinder pressure gauge. Use a wrench to avoid manual rotation during installation. Use an O-ring at the connection between the pressure gauge and the oil cylinder;
6. The first time the oil cylinder runs, the motor of the hydraulic station should be rotated clockwise (indicated on the motor). When the oil cylinder is pushed forward, the pressure gauge base should discharge air, and the oil cylinder should be repeatedly pushed forward and backward (the upper limit pressure of the pressure gauge is 10Mpa) and air should be discharged simultaneously;
7. The filter press runs for the first time, select the manual state of control cabinet to run different functions respectively; After the functions are normal, you can select the automatic state;
8. Installation of filter cloth. During the trial operation of the filter press, the filter plate should be equipped with filter cloth in advance. Install the filter cloth on the filter plate to ensure that the filter cloth is flat and there are no creases or overlaps. Manually push the filter plate to ensure that the filter cloth is flat.
9. During the operation of the filter press, if an accident occurs, the operator presses the emergency stop button or pulls the emergency rope;
✧ Main faults and troubleshooting methods
Fault phenomenon | Fault Principle | Troubleshooting |
Severe noise or unstable pressure in the hydraulic system | 1、The oil pump is empty or the oil suction pipe is blocked. | Oil tank refueling, solve suction pipe leakage |
2、The sealing surface of the filter plate is caught with misc. | Clean sealing surfaces | |
3、Air in the oil circuit | Exhaust air | |
4、Oil pump damaged or worn | Replace or repair | |
5、The relief valve is unstable | Replace or repair | |
6、Pipe vibration | Tightening or reinforcing | |
Insufficient or no pressure in the hydraulic system | 1、Oil pump damage | Replace or repair |
|
recalibration | |
3、Oil viscosity is too low | Replacement of oil | |
4、There is a leak in the oil pump system | Repair after examination | |
Insufficient cylinder pressure during compression | 1、Damaged or stuck high pressure relief valve | Replace or repair |
2、Damaged reversing valve | Replace or repair | |
3、Damaged large piston seal | replacement | |
4、Damaged small piston "0" seal | replacement | |
5、Damaged oil pump | Replace or repair | |
6、Pressure adjusted incorrectly | recalibrate | |
Insufficient cylinder pressure when returning | 1、Damaged or stuck low pressure relief valve | Replace or repair |
2、Damaged small piston seal | replacement | |
3、Damaged small piston "0" seal | replacement | |
Piston crawling | Air in the oil circuit | Replace or repair |
Serious transmission noise | 1、Bearing damage | replacement |
2、Gear striking or wearing | Replace or repair | |
Serious leakage between plates and frames |
|
replacement |
2、Debris on sealing surface | Clean | |
3、Filter cloth with folds, overlaps, etc. | Qualified for finishing or replacement | |
4、Insufficient compression force | Appropriate increase in compression force | |
The plate and frame are broken or deformed | 1、Filter pressure too high | turn down the pressure |
2、High material temperature | Appropriately lowered temperatures | |
3、Compression force too high | Adjust the compression force appropriately | |
4、Filtering too fast | Reduced filtration rate | |
5、Clogged feed hole | Cleaning the feed hole | |
6、Stopping in the middle of filtration | Do not stop in the middle of filtration | |
The replenishment system works frequently | 1、The hydraulic control check valve is not tightly closed | replacement |
2、Leakage in the cylinder | Replacement of cylinder seals | |
Hydraulic reversing valve failure | Spool stuck or damaged | Disassemble and clean or replace the directional valve |
The trolley can't be pulled back because of the back and forth impact. | 1、Low oil motor oil circuit pressure | adjust |
2、The pressure relay pressure is low | adjust | |
Failure to follow procedures | Failure of a component of the hydraulic system, electrical system | Repair or replace symptomatically after inspection |
Diaphragm damage | 1、insufficient air pressure | Reduced press pressure |
2、Insufficient feed | Pressing after filling the chamber with material | |
3、A foreign object has punctured the diaphragm. | foreign matter removal | |
Bending damage to main beam | 1、Poor or uneven foundations | Refurbish or redo |